A Comprehensive Guide to the Refine and Advantages of Plastic Extrusion
In the substantial world of manufacturing, plastic extrusion emerges as a crucial and very reliable procedure. Altering raw plastic into continual accounts, it caters to a variety of markets with its exceptional versatility.
Comprehending the Fundamentals of Plastic Extrusion
While it might appear complex initially glimpse, the procedure of plastic extrusion is basically easy - plastic extrusion. It is a high-volume production technique in which raw plastic is thawed and formed right into a constant account. The process starts with the feeding of plastic material, in the type of pellets, powders, or granules, right into a warmed barrel. The plastic is then thawed making use of a mix of heat and shear, used by a revolving screw. As soon as the molten plastic gets to completion of the barrel, it is forced through a small opening understood as a die, shaping it into a desired form. The shaped plastic is after that cooled, strengthened, and cut into wanted sizes, finishing the process.
The Technical Refine of Plastic Extrusion Explained
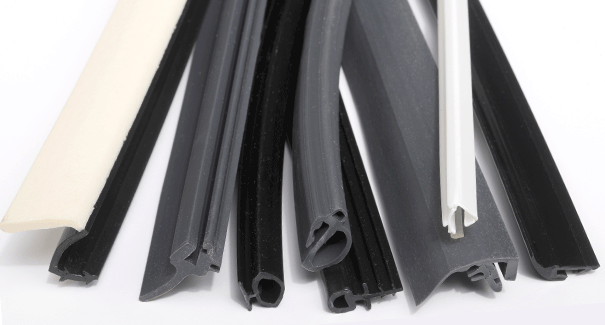
Kinds Of Plastic Suitable for Extrusion
The choice of the appropriate kind of plastic is a vital facet of the extrusion procedure. Various plastics offer unique homes, making them a lot more fit to specific applications. Comprehending these plastic kinds can considerably boost the extrusion procedure.
Comparing Plastic Extrusion to Various Other Plastic Forming Approaches
Understanding the types of plastic appropriate for extrusion leads the way for a more comprehensive discussion on how plastic extrusion piles up against other plastic creating methods. Plastic extrusion is exceptional when it comes to creating continuous profiles, such as seals, pipes, and gaskets. It additionally allows for a regular cross-section along the length of the product.
Key Advantages of Plastic Extrusion in Production
In the realm of manufacturing, plastic extrusion supplies lots of considerable benefits. One noteworthy advantage is the cost-effectiveness of the process, which makes it an economically attractive manufacturing approach. In addition, this technique provides exceptional item see here now versatility and enhanced production rate, thus boosting overall manufacturing effectiveness.
Cost-Effective Production Approach
Plastic extrusion leaps to the forefront as an economical production technique in production. This process stands out for its capability to produce high quantities of material promptly and successfully, providing manufacturers with significant savings. The primary price benefit is the capability to use more economical raw materials. Extrusion makes use of thermoplastic materials, which are less pricey contrasted to ceramics or metals. Additionally, the extrusion procedure itself is relatively basic, minimizing labor prices. Furthermore, plastic extrusion calls for less power than conventional production methods, contributing to lower operational expenses. The procedure likewise reduces waste, as any type of faulty or excess materials can be recycled and recycled, offering an additional layer of cost-effectiveness. Generally, the monetary benefits make plastic extrusion an extremely attractive option in the production sector.

Superior Item Flexibility
Past the cost-effectiveness of plastic extrusion, an additional substantial advantage in making lies in its premium item adaptability. This makes plastic extrusion an excellent service for industries that call for customized plastic parts, such as vehicle, building and construction, and packaging. In essence, plastic extrusion's product versatility cultivates development while enhancing functional efficiency.
Boosted Manufacturing Speed
A considerable benefit of plastic extrusion lies in its improved production speed. Couple of other manufacturing procedures can Continued match the speed of plastic extrusion. In addition, the ability to maintain constant high-speed manufacturing without compromising item quality establishes plastic extrusion apart from other approaches.
Real-world Applications and Influences of Plastic Extrusion
In the realm of production, the strategy of plastic extrusion holds extensive significance. This procedure is commonly used in the manufacturing of a variety of items, such as plastic tubing, window frameworks, and weather condition removing. As a result, it considerably affects industries like imp source building, packaging, and automotive industries. Furthermore, its impact expands to daily things, from plastic bags to tooth brushes and disposable cutlery. The economic benefit of plastic extrusion, mainly its high-volume and cost-efficient outcome, has actually changed manufacturing. The environmental effect of plastic waste stays a concern. Therefore, the industry is constantly pursuing innovations in eco-friendly and recyclable materials, showing a future where the benefits of plastic extrusion can be maintained without endangering ecological sustainability.
Conclusion
To conclude, plastic extrusion is a very efficient and effective approach of transforming basic materials into varied products. It provides various advantages over other plastic developing approaches, consisting of cost-effectiveness, high result, very little waste, and layout adaptability. Its impact is profoundly really felt in different industries such as building and construction, vehicle, and durable goods, making it a pivotal procedure in today's production landscape.
Digging much deeper into the technological procedure of plastic extrusion, it starts with the option of the ideal plastic product. Once cooled down, the plastic is reduced right into the called for lengths or injury onto reels if the product is a plastic movie or sheet - plastic extrusion. Comparing Plastic Extrusion to Other Plastic Forming Approaches
Understanding the types of plastic ideal for extrusion paves the means for a wider discussion on how plastic extrusion stacks up versus other plastic forming techniques. Couple of various other manufacturing procedures can match the rate of plastic extrusion.
Comments on “Advanced plastic extrusion solutions for manufacturers”